DTF Powder Curing Methods
Cost-Effective Solutions for All Print Shops
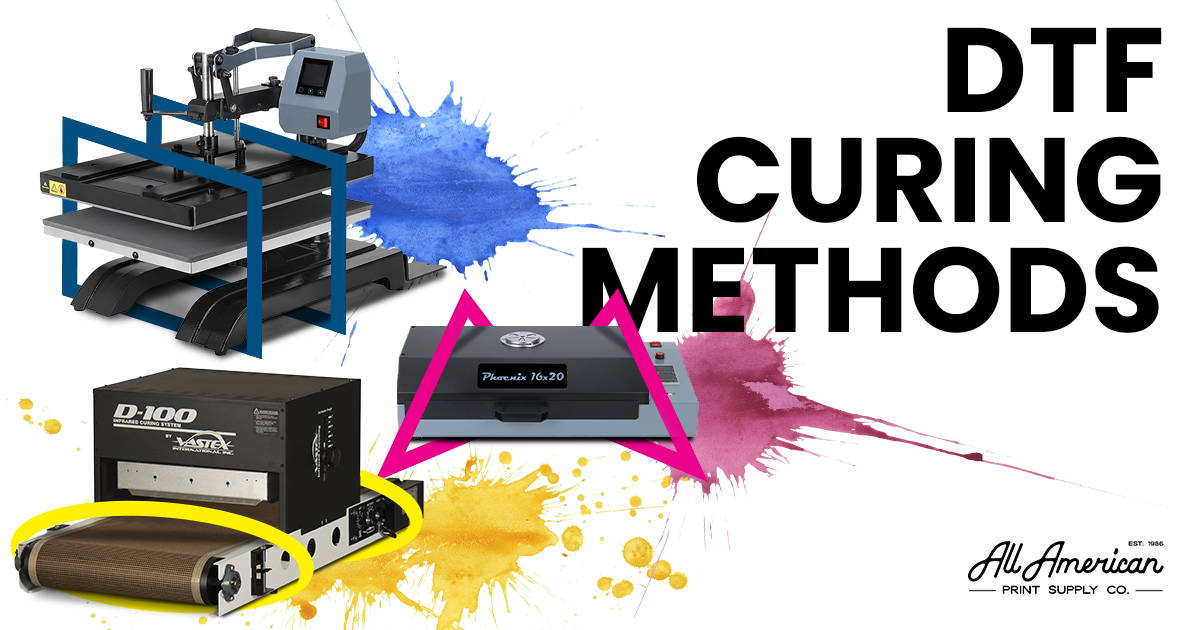
"Heat is required to forge anything. Every great accomplishment is the story of a flaming heart."
Want to kickstart your printing journey with DTF (direct-to-film) transfers? We'll guide you through the essential process of curing the powder used in DTF printing. For those venturing into DTF for the first time, curing the powder is a crucial step that requires the right equipment and techniques. And for those of you already familiar with DTF printing, you might discover some cost-effective curing methods you haven't considered before.
Curing DTF (direct-to-film) powder transfers is an essential step in the printing process. While specialized equipment like heat presses, conveyor dryers, and shaker/dryer units are commonly recommended, there are other cost-effective methods that you might already have in your workspace.
Flash Cure Dryer
Screen printers may have a flash cure dryer like the Vastex F1000with a rotary table and vented pallets. By setting it to high heat and monitoring for 30-45 seconds, you can achieve fast curing. Flash cure dryers are relatively hands-free and efficient, but the size and height may limit your film dimensions. Flash cure dryers are moderately expensive for DTF curing but can be a worthwhile investment for larger print shops. They have a larger footprint than heat presses and may require more dedicated space in a workshop. However, they are generally easy to operate, with minimal setup and monitoring required for DTF curing.
Conveyor Dryer
A conveyor dryer like the Vastex D-100 is a versatile and efficient option for curing DTF transfers. Simply place your powdered film on the belt, and it'll be cured as it passes through the dryer. Conveyor dryers are more expensive than other options but offer increased productivity, especially for larger volumes. They are also larger in size, requiring a significant amount of space in a workshop. However, their automated nature makes them incredibly easy to use for DTF curing, with minimal hands-on effort required once set up correctly.
Curing Oven
In our opinion, a curing oven like the Phoenix Air 16x20 is the best option for curing DTF transfers. It's designed specifically for this purpose and provides uniform, contact heating for better adhesion. You can load your powdered film, set the timer, and continue with other production tasks while it cures. This frees up your heat press for continued transferring, maximizing efficiency (and profits!). Curing ovens are relatively expensive but offer a dedicated solution for DTF curing. They have a moderate footprint, similar to a large oven, and can be easily accommodated in most workshops. In terms of ease of use, curing ovens are straightforward, with simple controls and minimal monitoring required during the curing process.
DTF Shaker & Dryer
Dedicated DTF shaker & dryer units are another specialized option for curing powder transfers. These all-in-one machines combine shaking and heating functions to efficiently cure the DTF powder. While they are designed specifically for DTF curing, they can be quite expensive, especially for smaller operations. However, they offer a compact footprint and are incredibly easy to use, with automated shaking and curing cycles. For high-volume DTF production, a shaker & dryer unit can be a worthwhile investment, providing consistent results and maximizing efficiency.
There are several methods available for curing DTF powder transfers, each with its own advantages and considerations. Whether you're a small shop or a large-scale operation, it's important to evaluate your specific needs, budget, and workspace constraints. From cost-effective options like heat presses to specialized equipment like conveyor dryers and curing ovens, choosing the right curing method can streamline your DTF printing process, improve efficiency, and ultimately enhance your profitability. Regardless of the method you choose, be sure to thoroughly test and adjust settings to achieve optimal results for your DTF transfers.