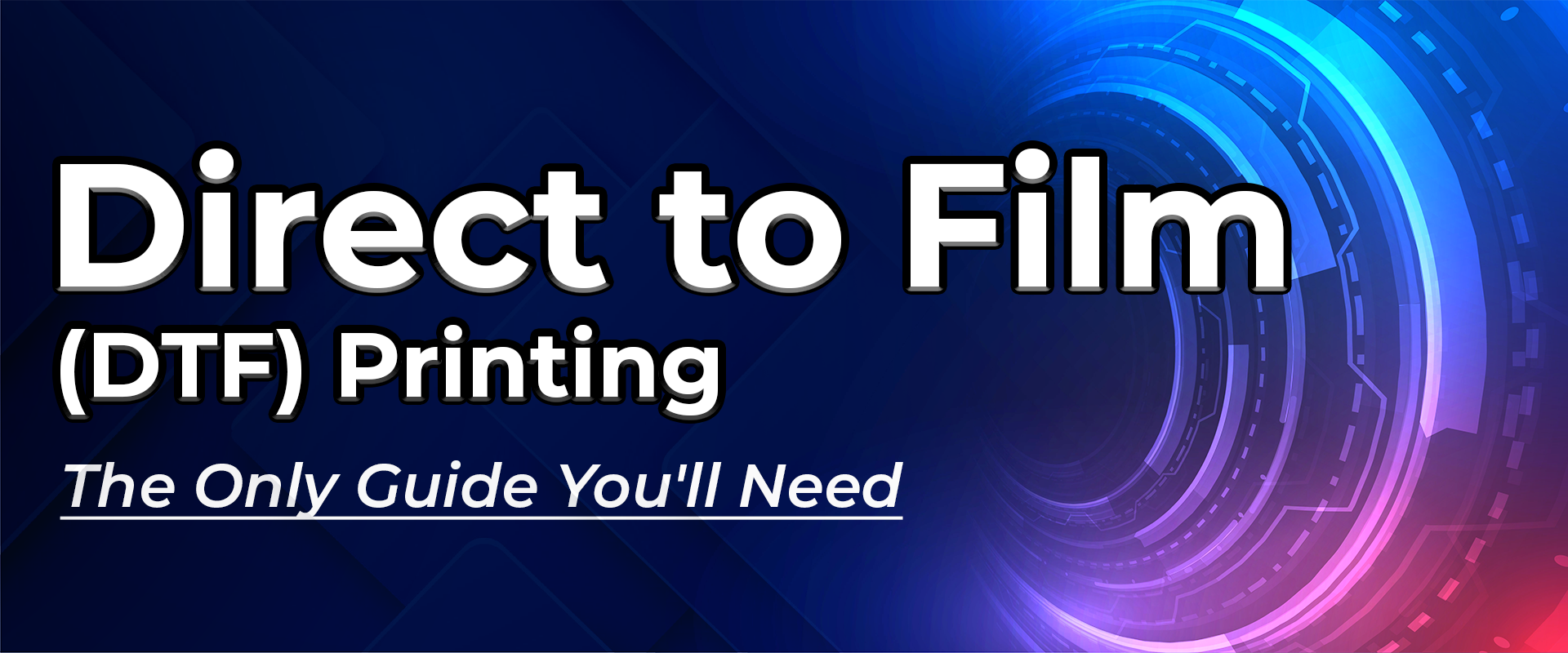
Direct to Film (DTF) Printing - The Only Guide You'll Need
You may have heard of a new technology recently and its many terms such as, “DTF”, “Direct to Film”, “DTG Transfer”, "Direct-to-Garment Transfer", and more. For the purpose of this blog, we’ll be referring to it as “DTF”. You may be wondering what is this so-called DTF and why is it getting so popular? Here we’ll do a deep dive on what DTF printing is, who it’s for, benefits and drawbacks, and more!
Direct to Film (also known as DTF) is exactly what it sounds like. You print an artwork on a special film and transfer said film onto fabric or other textiles.
Benefits
Versatility on Materials
- DTF can be applied on a wide range of materials including, cotton, nylon, treated leather, polyester, 50/50 blends and more (light and dark fabrics).
Cost Effective
- Can save up to 50% white ink.
- Supplies are also significantly more affordable.
No Pretreat Required
- If you are coming from a direct-to-garment (DTG) background, you must be familiar with pretreating the garments before printing. With DTF, you no longer have to worry about pretreating the garment prior to printing.
No A+B Sheets Marrying Process
- If you come from a white toner laser printer background, you’ll be pleased to hear that DTF doesn’t require the marrying process of expensive A+B sheets.
Production Speed
- Since you essentially take out a step of pretreating, you’re able to speed up production.
Washability
- Has been proven through testing to be equal to if not better than traditional direct-to-garment (DTG) printing.
Easy Application
- DTF allows you to apply the artwork on difficult/ awkward parts of the garment or fabric with ease.
High Stretchability and Soft Hand Feel
No Scorching
Drawbacks
- Full size prints don’t come out as great as direct-to-garment (DTG) prints.
- Different hand feel compared to direct-to-garment (DTG) prints.
- Must wear safety equipment (protective eyewear, mask, and gloves) when working with DTF products.
- Must keep the DTF adhesive powder in a cool temperature. High humidity can cause quality issues.
Pre-Requisites for Your First DTF Print
- Like we mentioned above, DTF printing is extremely cost-effective and therefore, doesn’t require a sizable investment.
- There are dtf printers that are specifically made for direct to film.
- We have heard from some of our customers that they use their direct-to-garment (DTG) printers or modify a printer for DTF purposes.
- You will be printing directly on the film, hence the process name “direct-to-film”. DTF films are available in either cut sheets and rolls.
Software
- You are able to use any direct-to-garment (DTG) software. However, the Kothari Neo Rip allows for additional benefits, which will make your life much easier. You will be able to adjust the white levels on your prints, so you’ll be left with a soft hand feel without sacrificing quality.
- This DTF powder acts as the “glue adhesive” that binds the print to the fabric of your choosing.
- We recommend using dtf ink that compatible with your dtf printer so there's no clogging or other issues.
- Depending on the printer you're using, direct-to-garment (DTG) or any textile inks will work.
- A heat press provides even heat distribution and consistent pressure, which are crucial for a durable and vibrant transfer of your DTF prints onto fabric.
- By maintaining the necessary temperature and pressure, a heat press ensures that your DTF prints adhere properly, giving you professional-quality results every time.
As you grow your business and/ or want to speed up your workflow, these equipment will optimize your workflow.
DTF Air Purifier
- We would highly recommend having this as part of your workflow; however, it is not required. It helps with ventilation of when you're curing the dtf powder and is able to absorb and filter out any gases or dust.
DTF Curing Oven
- A DTF curing oven/ DTF dryer is optional to melt the dtf powder to make your production even faster. It'll also melt your dtf powder more uniform, which will allow for a stronger adhesion.
DTF Powder Shaker Machine/ DTF Dryer
- You can get these separately as needed or there are many DTF Powder Shaker Machines that also has a dryer built in with it. With the DTF shaker dryer, you no longer will have to manually shake the powder on the print yourself. Simply load the sheets, apply powder and the dtf powder machine will shake the excess for you.
- If you opt for the ones with the DTF dryer built in, it'll automatically place the dtf film onto the dryer to be cured.
Process
If you'd rather watch a video instead, we created a simple, easy to follow video on the Direct to Film (DTF) process! Although this video won't include the optional equipment as part of the process, we'll have that below.
Step 1 - Print on Film
- You must print your CMYK down first, then your white layer afterwards (which is the opposite of direct-to-garment (DTG). This can be done easily with the Kothari Neo Rip software in one pass. Other softwares will require you to run the print twice to accomplish this.
Step 2 - Apply Powder (Either Manually or with DTF Shaker Machine)
- Apply the powder uniformly while the print is still wet to ensure it sticks. Carefully shake off the excess powder so there’s no remaining other than the print. This is extremely important as this is the glue that holds the print to the fabric.
- If you have a dtf powder shaker machine, you'll normally place your print, add the powder, and let the machine work its magic.
Step 3.0 - Turn on and Adjust Air Purifier (Optional)
- Adjust your dtf air purifier so it's above or near where the steam/ vapor comes out of from where the machine you'll be curing from (either dtf curing oven, heat press, or dryer).
Step 3.1 - Melt/ Cure the Powder
- Curing Oven: Place your print onto the curing oven with the temperature recommended by your curing oven manufacturer.
- Heat Press: Cure your newly powdered print by hovering with your heat press at 350 degrees Fahrenheit for 2 minutes.
Step 4 - Transfer
- Now that the transfer print is cooked, you are ready to transfer it onto the garment. Use your heat press to transfer the print film at 284 degrees Fahrenheit for 15 seconds.
Step 5 - Cold Peel/ Hot Peel
- Depending on what type of dtf transfer film you're using, you will either have to wait until the print is completely cooled off or can peel off while it's still hot before peeling the carrier sheet off the garment or fabric. Please read instructions of your specific dtf film.
Overall Thoughts
- While direct to film printing is not positioned to overtake direct-to-garment (DTG) printing, this process can add an entirely new vertical to your business and production options. Through our own testing, we have found that using DTF printing for smaller designs (that are difficult with direct-to-garment printing) works best, such as neck labels, chest pocket prints, etc.
- If you own a direct-to-garment printer and are interested in DTF, you should definitely give it a try given its high upside potential and cost-effectiveness.
For more information on any of these products or processes, feel free to check out this page or to give us a call at 714-576-2900 – be sure to check out our YouTube channel for walkthroughs, tutorials, product spotlights, webinars and more!