What About Powders?
DTF What To Know: Hot Melt Powder

"Lesson learned. Wisdom earned."
Welcome back to another installment of our DTF What To Know handbook. Direct to film continues to stabilize further, and we're witnessing a significant spike in printer sales. This surge can be attributed, in part, to the DTF Station Prestige A4 desktop direct to film printer. Never before has such high quality been available at such a low price, serving as a gateway to DTF for many transitioning from vinyl or sublimation backgrounds. In this series, we're delving into the fundamentals in a 101-style introduction, getting to know all the key components. Despite DTF involving a relatively straightforward process, one of the crucial aspects is the hot melt powder. Let’s talk about it.
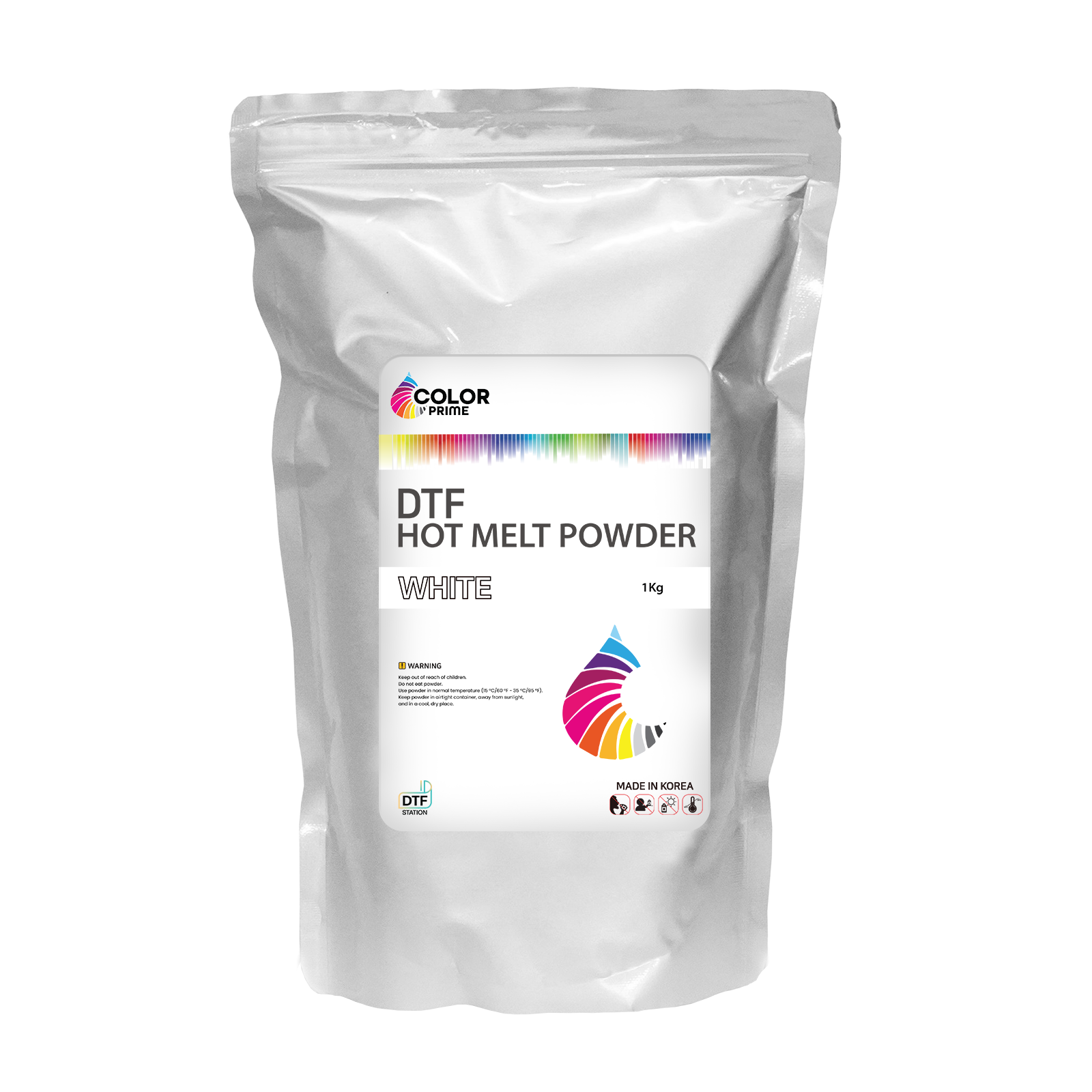
WHAT IS HOT MELT POWDER?
Before we explore what the hot melting powder does, let's first address what it actually is. In a literal sense, think of the hot melt powder as finely ground plastic—almost sand-like. The powder is measured in GSM (Grams per Square Meter) and typically falls in the 120 range. This special adhesive powder is used for bonding materials like fabrics or textiles. Its value lies in high durability, elasticity, water resistance, and superior cost efficiency compared to conventional adhesives.
A good powder should be safety-tested and certified with an OEKO-TEK passport, indicating no risk of air pollution or exposure to toxicity during the production/application process. For safety purposes, wearing gloves or protective eyewear, especially if you have sensitive skin, might be advised. Once melted down to a specific temperature range, this powder serves as a robust bonding agent for applications requiring lasting adhesion.
HOW DOES IT WORK
Direct to film transfers won't apply without melting powder. Single-piece, small-run sheets, or direct-to-garment machine-printed DTF transfers can be applied by hand or with a dedicated powdering machine. In a production setting, a roll-to-roll powder machine is far more efficient. Printed images on a film roll are fed into a powdering station where the adhesive is applied to the wet print. The powdered film is then agitated to remove excess around the image and fed into a conveyor dryer for curing. The prints can wait a bit before powder application, allowing the ink to be tacky enough for a secure hold. Once the powder is dried to the print via heat, the printed transfer is ready to be pressed, stored, shipped out, or sold as a service.
BLACK POWDER?
This past summer, we covered what dye migration is, how it can affect our final product, and the role black melting powder can play to prevent this. Dye migration occurs when the fabric color or pattern sublimates into your print, distorting it. Black powder is a proven dye blocker, offering an easy fix if you encounter dye migration during your DTF process. It's worth mentioning that the DTF Station line of Prestige direct-to-film printers provides white ink layer control to prevent migration.
Ensure you're subscribed to the newsletter for more helpful tips to aid you in your direct-to-film journey.
Meet our author
Estevan Romero
Brand Marketing Lead
Esteven Romero began making YouTube videos back in 2017 to help new business owners learn how to use their products and grow their operation.
He has been featured in many companies content such as Siser North America, Key Print Co and more. He has been featured as a speaker/presenter nationwide across the tradeshow circuit sharing information and insight to the print community audience and brings 13+ years of experience to the table.
You can meet Estevan and more of the friendly All American Print Supply Co team by visiting the company live events calendar and our YouTube channel.