From Blank to Beautiful
The Art of UV DTF Printing
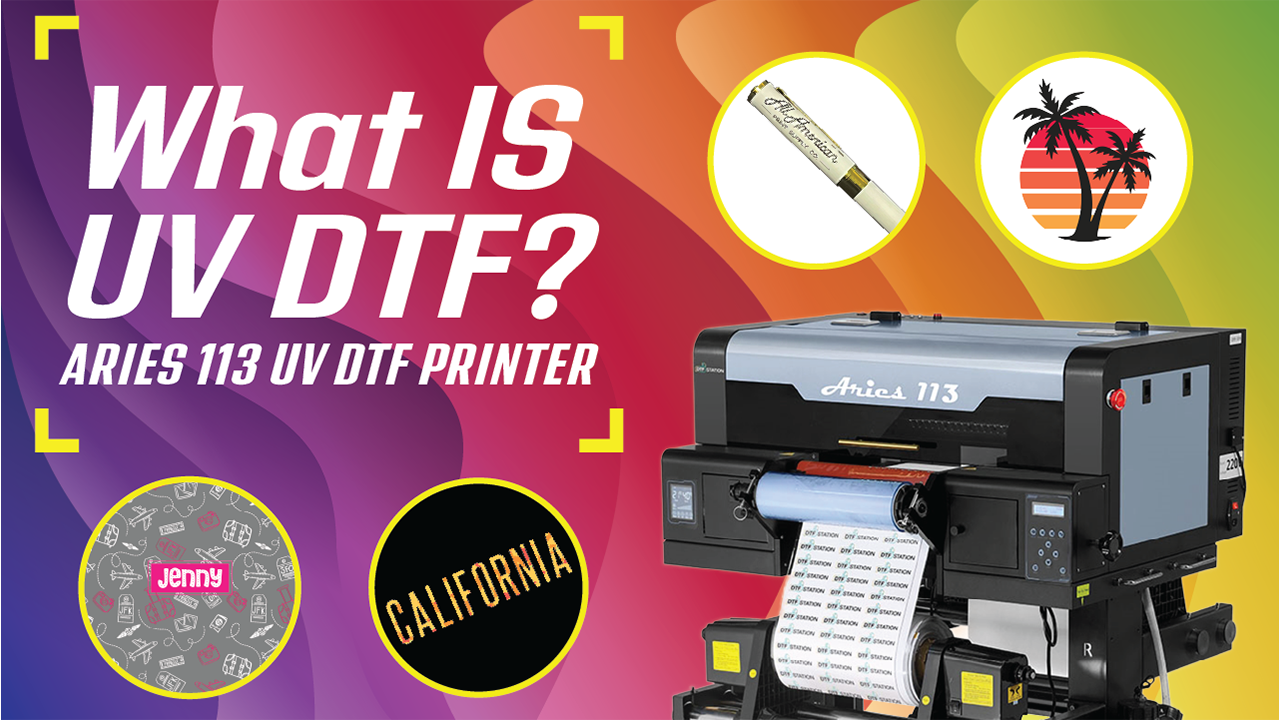
“The next generation has always been and will be better than the previous one.”
What is UV DTF Printing?
Have you ever wondered how those awesome designs you see on metal, leather, wood, plastic, ceramic, and glass are applied? Well, they're made by UV DTF printing. "UV DTF what?" you might ask. UV DTF stands for Ultraviolet Direct to Film printing. UV DTF printing is a cutting-edge technique that's taking the DTF printing industry by storm!
Ultraviolet DTF Printing and its Benefits
One of the coolest things about UV DTF printing is its versatility. UV DTF printing uses similar materials and equipment as UV printing but offers broader possibilities, including:
Durability: You can rest easy that your print projects are resistant to fading, scratching, and weathering, guaranteeing long-lasting designs that withstand wear and tear, unlike solvent-based inks.
Environment Friendly: UV-cured inks emit minimal volatile organic compounds (VOCs), making Ultraviolet Printing a greener option for eco-conscious businesses.
Wider Range of Materials: UV DTF printing can be applied directly and easily to hard-surface objects, especially items with beveled or cylindrical shapes like mugs and bottles. However, it is not suitable for fabrics.
Higher Production Volume: UV printing is limited in size and quantity by the application surface, resulting in relatively small print runs. In contrast, UV DTF transfers can produce large quantities of crystal stickers simultaneously that can then be transferred to a wider range of substrates.
Cost Effective: With its rapid curing process, UV Printing streamlines production, reducing labor costs and increasing efficiency.
High Definition Prints, All the Time:
Ultraviolet printing delivers high-definition prints with vibrant colors and precise details, ensuring your designs stand out. You can be sure of high-quality digital prints all the time.
It starts with design creation: you create or select your desired design using proprietary design software, also known as RIP. Then comes the film printing; you print the design onto a special DTF film using UV printing technology. Next is the film transfer; heat and pressure are applied to transfer the printed design from the film onto the object, ensuring adhesion and durability. Lastly, curing - the transferred designs are cured using UV lights to ensure optimal color retention and longevity.
Ultraviolet ink, unlike traditional inks, contains special chemicals that react to ultraviolet light. This means that when the ink is exposed to UV light, it instantly dries and hardens, creating a strong bond with the material.
But why use a film, you ask? Well, the film serves as a carrier for the ink, ensuring precise and detailed prints. Plus, it allows for easy handling and storage of the designs before transferring them onto the printing material.
Costs, Maintenance, and Energy Consumption
Is it really economical?
Cost-wise, UV DTF printing can be a bit pricier upfront compared to traditional methods. You'll need to invest in a UV DTF printer, which can range from a few thousand to tens of thousands of dollars, depending on the model and features. Additionally, there are costs associated with UV ink, DTF film, and other supplies.
But don't let that scare you off! While the initial investment may seem steep, UV DTF printing offers significant long-term savings. The prints are incredibly durable and resistant to fading, meaning you won't have to constantly reprint.
How about parts and maintenance?
In terms of ongoing costs, you'll need to budget for replacement parts and consumables, such as printheads and cleaning solutions. However, these costs are generally manageable and are outweighed by the benefits of UV DTF printing.
Now, let's talk about maintenance. Keeping your UV DTF printer in tip-top shape is crucial for optimal performance and longevity. Luckily, maintenance is relatively straightforward. Regularly cleaning the printer and ensuring proper calibration are key to preventing clogs and other issues.
Another thing to consider is energy consumption. UV DTF printers typically use UV lamps to cure the ink, which can be energy-intensive. However, advancements in technology have led to more energy-efficient printers, helping to reduce operating cost
UV DTF PRINTING vs Other Print Methods: Pros and Cons
DTF vs UV DTF
There is no difference in the application surfaces between DTF (direct-to-film) printing and UV DTF printing, as they refer to the same printing technology. DTF and UV DTF are two different terms used to describe the same process:
DTF (Direct-to-Film) Printing: Involves printing a design using specialized inks onto a transparent film. The printed film is then transferred to the final substrate using a heat press. It can adhere to a wide variety of surfaces like cotton, polyester, nylon, leather, wood, metal, etc.
UV DTF Printing: UV inks are cured/dried immediately after printing using UV light. The UV-printed design is then transferred from the film to the final substrate via heat press.
So, in essence, DTF and UV DTF describe the same printing method, with UV DTF specifically highlighting the use of UV-curable inks. The key aspect is that both DTF and UV DTF allow for printing designs onto an intermediary transparent film, which can then be heat applied to virtually any substrate material and surface texture, including:
Textiles (cotton, polyester, blends, etc.)
Leather/Faux Leather
Wood
Metals
Rigid Plastics
And more.
This versatility in being able to transfer onto diverse surfaces is the core advantage of the DTF/UV DTF process compared to more limited printing methods like direct-to-garment.
DTG vs UV DTF
DTG printing involves printing designs directly onto fabric using specialized inkjet printers. The advantages and differences are the following:
Application Surface: DTG printing is done directly onto the garment fabric, most commonly cotton, cotton blends, and some synthetic fabrics.
Surface Preparation: The garment surface needs to be relatively smooth and free of heavy textures or embroidery for best results.
DTG has more limitations on the types of fabrics and surfaces it can print on compared to DTF. Highly textured or synthetic fabrics can be challenging. While DTG prints directly on the garment fabric, DTF uses an intermediary film that can be applied to a broader array of surfaces, including textured or synthetic materials that are problematic for DTG. This makes DTF a more versatile printing method in terms of compatible application surfaces.
Sublimation vs UV DTF Printing
Sublimation printing involves transferring designs onto fabric using heat and pressure, which causes the ink to turn into a gas and penetrate the fabric's fibers. One of the main advantages and application differences of sublimation printing are:
Application Surface: Sublimation printing is done onto polyester or polymer-coated surfaces as the sublimation dyes need to be able to gasify into the substrate. While UV DTF printing uses a specialized UV ink printed onto a transparent film which is then heat transferred onto the final substrate.
Fabric Compatibility: Works best on 100% polyester or polyester-coated products like performance apparel, polyester hard goods, and polymer-coated surfaces.
UV DTF beats sublimation in the following:
Surface Versatility: DTF transfers can adhere to a wide variety of surfaces beyond just textiles - cotton, polyester, nylon, leather, wood, metal, rigid plastics, and more.
Texture Capability: DTF can print on highly textured fabrics and patterned surfaces that sublimation cannot easily adhere to.
Surface Treatment: Some surfaces may require an adhesive powder or polymer coating pre-treatment for better adherence of the DTF transfer film.
In essence, sublimation is limited to polyester or polymer-coated substrates, while UV DTF has much greater versatility for adhering to diverse surfaces including cotton, blends, textures, hardgoods, and more. However, sublimation offers superior wash durability compared to DTF transfers on polyester fabrics.
The choice depends on the desired products and substrates - sublimation for polyester apparel/goods, and DTF for applying full-color prints across a broader range of surfaces beyond just polyester.
Is UV DTF Printing the best option for you?
It depends on your specific needs and budget. UV DTF printing excels in object customization. The crystal stickers it produces can be applied to most objects, including those with irregular shapes, and can be produced in batches, significantly enhancing production efficiency.
Despite these advantages, UV DTF printing can involve more operational steps, more moving parts, and higher upfront costs compared to some other printing methods.
At the end of the day, it's all about finding the right fit for your business. Whether you choose UV DTF printing or another method, the key is to do your research and weigh your options carefully.